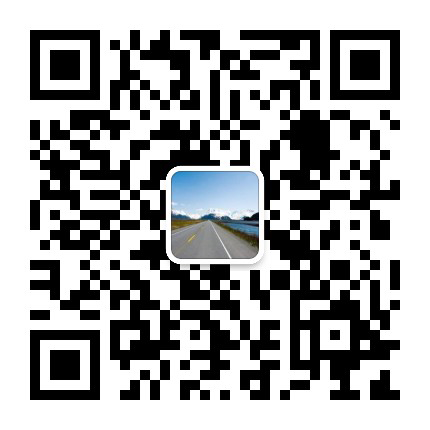
高溫、噪音和油味與工業(yè)制造的關(guān)系就像陰和陽一樣密不可分。但是在Toolcraft的玻璃生產(chǎn)車間中,情況已不再如此。在入口處出示員工ID并進(jìn)入工廠后,工人聽不到任何噪音。但在十二個(gè)3D打印機(jī)的每一個(gè)小窗口中,都可以觀察到激光束在一層層的金屬粉末中化為一道耀眼的光。
“每當(dāng)新技術(shù)主導(dǎo)市場時(shí),會(huì)有很多問題隨之而來,其中之一便是質(zhì)量保證?!盝ens Heyder指著顯示器上由ZEISS Axio Imager光學(xué)顯微鏡拍攝并被放大50倍的兩幅圖像說道。“左圖顯示的是一個(gè)良好的組件,但右側(cè)圖像包含空腔和焊縫缺陷?!? Heyder一直在Toolcraft材料實(shí)驗(yàn)室中擔(dān)任材料技術(shù)員,他表示:“在高應(yīng)力下,這可能會(huì)導(dǎo)致裂紋。”然而,材料實(shí)驗(yàn)室只是 Toolcraft端到端質(zhì)量保證過程組成部分之一。
蔡司三坐標(biāo)助力Toolcraft在每個(gè)處理步驟之后進(jìn)行檢驗(yàn)并確保質(zhì)量。包含ZEISS Axio Imager和ZEISS Axio Zoom.V16 顯微鏡;ZEISS ACCURA、ZEISS CONTURA 和ZEISS DuraMax三坐標(biāo)測量機(jī)以及光學(xué)3D掃描儀。
Christoph Hauck表示:“蔡司是一家為整個(gè)增材制造流程鏈提供完整且一致數(shù)據(jù)的計(jì)量技術(shù)公司?!痹?005年,42歲的他在Toolcraft接觸到增材制造技術(shù)。那時(shí),該技術(shù)“仍需大量改進(jìn)”且僅適用于制造原型。如今,情況已改變。Toolcraft的組件符合航空航天和醫(yī)療技術(shù)行業(yè)的嚴(yán)格要求,它們與傳統(tǒng)制造的部件一樣高性能及耐用。
這些組件的制造和應(yīng)用也更加有效,為了證明這一點(diǎn),Hauck展示了一個(gè)定子導(dǎo)流葉片,該導(dǎo)流葉片引導(dǎo)氣流通過固定式燃?xì)廨啓C(jī)。葉片的彎曲形狀通過精細(xì)的模擬進(jìn)行了優(yōu)化,這在傳統(tǒng)加工條件下幾乎很難以同等成本制造。
質(zhì)量保證部主管Markus Miehling說:“為了掃描此類復(fù)雜的葉片幾何形狀,我們使用蔡司的葉片軟件模塊”。使用3D掃描儀可快速了解葉片輪廓形狀。
因此,Toolcraft的材料專家創(chuàng)建了自己的方法來確定金屬粉末的粒度分布和結(jié)構(gòu)。他們將粉末與環(huán)氧樹脂混合,然后將硬化的樣品的一部分進(jìn)行研磨并放在ZEISS Axio Zoom.V16 顯微鏡下進(jìn)行檢驗(yàn)。
3D打印部件在接觸式測量時(shí)同樣需要進(jìn)行特殊處理。通過3D打印直接制造的部件可能會(huì)殘留固體粉末顆粒,比較粗糙,無法進(jìn)行掃描,只能使用測針測量單個(gè)點(diǎn),而不是通過接觸式測量整個(gè)部件表面。
如果部件沒有問題,則將其分配給切削技術(shù)人員,通過轉(zhuǎn)動(dòng)螺紋,使用切削技術(shù)優(yōu)化半徑并“精煉”表面。然后,再次在ZEISS ACCURA上測量組件時(shí),可以使用掃描式測頭。通過配備了ZEISS mass技術(shù)的三坐標(biāo)測量機(jī),使操作員可以在不同的測頭(包括光學(xué)單行測頭)之間快速切換。
Toolcraft 已經(jīng)使用了蔡司三坐標(biāo)增材制造產(chǎn)品線中的許多設(shè)備,但其 “設(shè)備庫”尚未配備掃描電子顯微鏡或工業(yè)CT。Christoph Hauch說,他們不知道未來會(huì)購買什么設(shè)備,但知道肯定會(huì)從蔡司三坐標(biāo)購買?!百|(zhì)量保證是增材制造的主要挑戰(zhàn),很高興知道我們擁有像蔡司這樣經(jīng)驗(yàn)豐富的合作伙伴。”